DABUPRINT
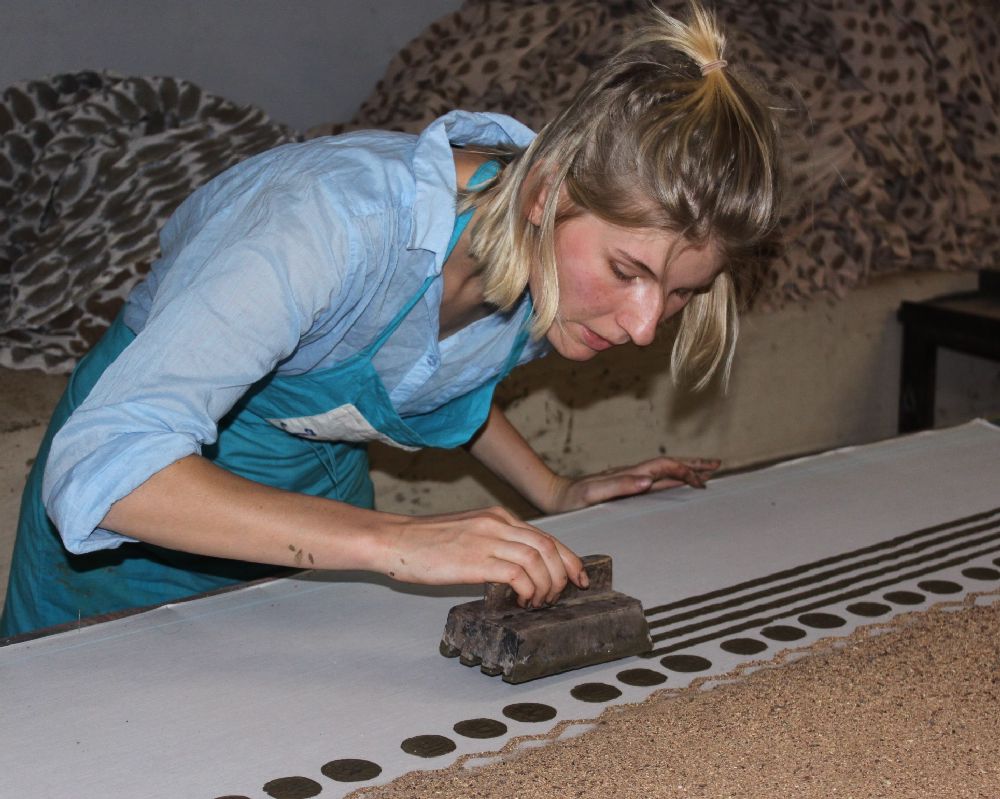
Dabu print is also known as resist print. Dabu print is the most famous print of Bagru print. To do dabuprint , first of all . the grey fabric is washed. After washing the fabric, the fabric is ready for printing. After this, the fabric is printed with a paste made of black mud. Natural ingredients are used to make this paste. To make Dabu paste, black mud is soaked in water, after that . wheat waste powder is added to it, which is called bidan in the local language. bidan is collected in the form of powder from the insects eating in the wheat warehouses, which is used to make Dabu paste. Tree gum and limestone are added to this paste. All these things are thoroughly mixed by digging with the feet. In this way, Dabu paste is prepared for printing.
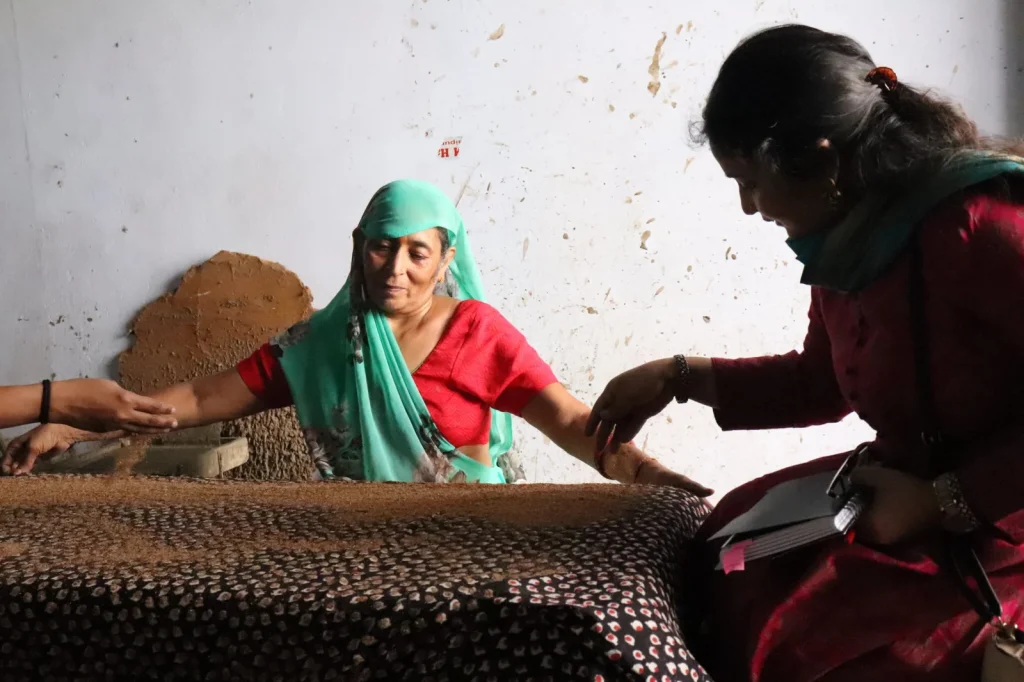
This paste is kept in a clay pot and printed with a wooden block. After printing, wood powder is sprinkled on the printed area so that the printed area where clay paste is applied dries up immediately and the paste does not stick to other parts of the cloth.
After this, the cloth is dried in the sun and natural dye is applied the next day

There are many types of natural dyes, some of the main dyes are as follows.
1. Indigo dye
2. Kassis
3. Harada dye
4. Naspal
INDIGO BLUE (NIL) MAKING PROCESS
Indigo blue is a blue colouring matter extracted from nil plants (indigofera tinctoria) . The dye stuff is obtained from the leaves .Freshly cut branches are spread in the water for some hours until the liquid becomes thick , slimy and yellowish brown .
The surface of this liquid is stirred and beaten ( by which oxygen is introduced ). It turns green , then blue and a thick sediment is formed . The liquid is brown off , and the sediment is heated and strained to produce a thick paste which is allowed to dry . It is made into cakes and dried , and then kept for use when required; such extraction of indigo is not done at present by the bagru printers . ready synthetic indigo granules are available in the market for use . The dye matter is not soluble in water . It is rendered soluble again by oxidation when it has penetrated the fibres .
The reduction is done by a long process of fermentation since ages and hence the term vatting . The reduced liquor is stored in the vat and is used from time to time . The method is still practised at bagru . Although improved knowledge of chemistry has made comparatively simpler methods possible , The fermentation method is believed to render the colour more lasting and more deep. ( In a chemical vat hydro sulphite of soda or hydros is used for reducing and caustic soda is used for dissolving the reduced indigo)
100 matka- full i.e abount 700 litres of water is filled in the old math (indigo vat ) to which 10 kgs of gothan ka chuna (Lime )is added . this is left for 15 days .
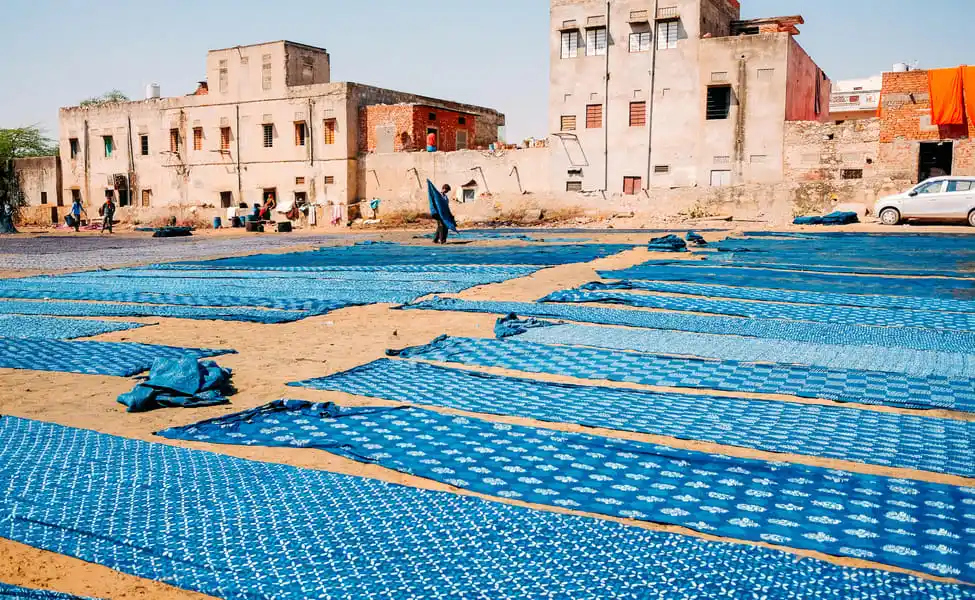
THE INDIGO DYEING (NIL KARNA ) PROCESS .
This is the process of cold dying . The cloth previously dyed with alizarin and subsequently printed with the resist paste is taken , piece by piece and treated in the stock indigo math . the operation consists of opening out the fold of the cloth , dipped vertically inside the math , so that it is completely immersed in the liquor , and then taking it out . this takes at onces a rich green colour. After this , the cloth is exposed to air whereby rapid oxidation takes place and the green colour turns to a deep blue shade in minutes . once again the same operation is repeated to give greater depth and uniformity to the colour . the printere wears dastana (rubber gloves ) while conducting this process .
2. Kassis
Natural dyes – Kashish, the key to sumptuous soft grey browns.
Kashish (potassium permanganate), a mineral produced from iron deposits (ferrous sulphate), works like a cold vat dye and creates a wonderful spectrum of grey, khaki, and brown shades.
The fabric is first dipped in a solution of water and harda (the yellow powder which is naturally occurring tannic acid) as a pretreatment to achieve lighter shades of brown. Darker shades can be achieved by adding boiled pomegranate rind to the harda solution. After the harda treatment, the fabric is dipped in the kashish solution (the green crystiline substance mixed with water).
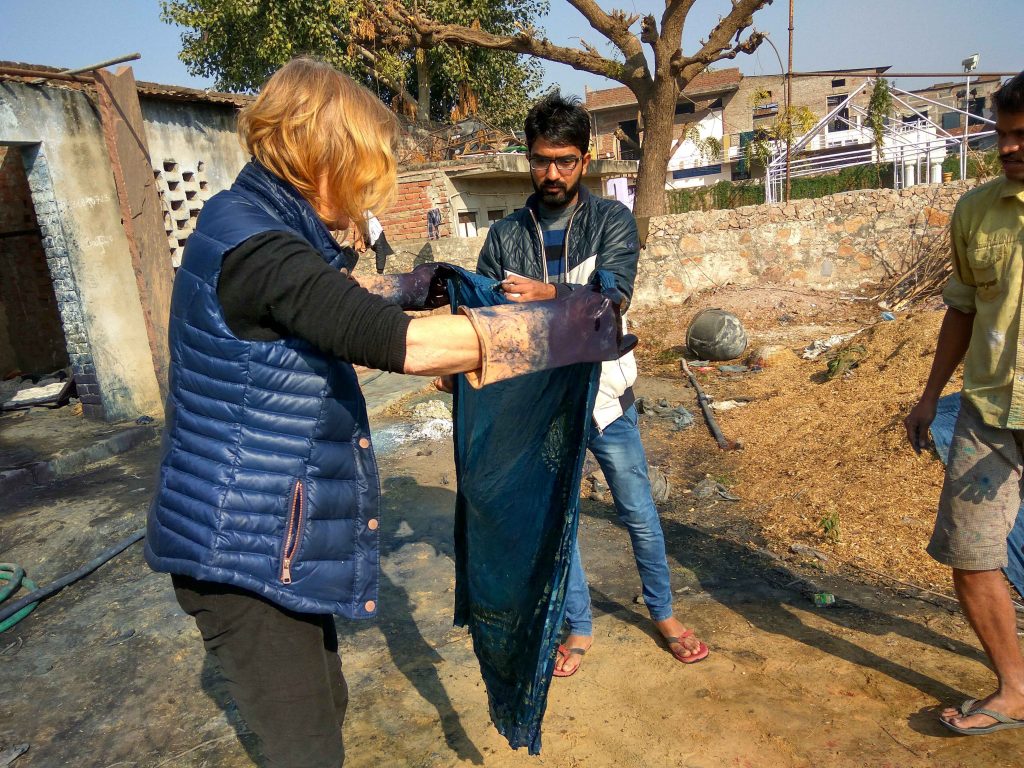
Harada dye
Pila karna solution:
Giving a primary creamish-yellow colour to the fabric, this solution acts as a mordant for the syahi paste. It is made of harda powder (Chebulic Myrobalan) in water. Near the wells or right on the edges of the Sanjaria river, holes are dug out to serve the purpose of tubs. These holes are covered with a thin layer of cloth and the harda powder and water are strained through the cloth to remove the suspended impurities. Harda powder is mixed in the proportion of about 50 gms. per metre of cloth. Sometimes mitha tel in the proportion of 50 gms. per 36 metres of cloth is added to the harda powder which is made into a paste and dissolved in water contained in the holes. This renders the cloth soft and pliable in the printing operation that follows and also helps in the uniform absorption of the printing paste to develop a rich shade.
The pila karna solution that is applied to the cloth after the alizarin dyeing to impart a fugitive creamish- yellow colour to the ground of the printed cloth is invvariably a solution of harda powder in water without any addition of oil .
4. Naspal
This is a decoction of the pomegranate rind obtained by boiling naspal (pomegranate rind )in water . 2.5 kg of naspal rind is boiled in water thoroughly so that the colouring matter of the naspal is fully extracted . This solution , which is sufficient for the treatment of 36 metres of cloth , is left overnight to cool down . The rinds of dry green pomegranates are used for the purpose . In place of naspal the craftsmen previously used the bark of dhawadi tree , which gave a faster colour . due to its scarcity ,naspal is presently being used .
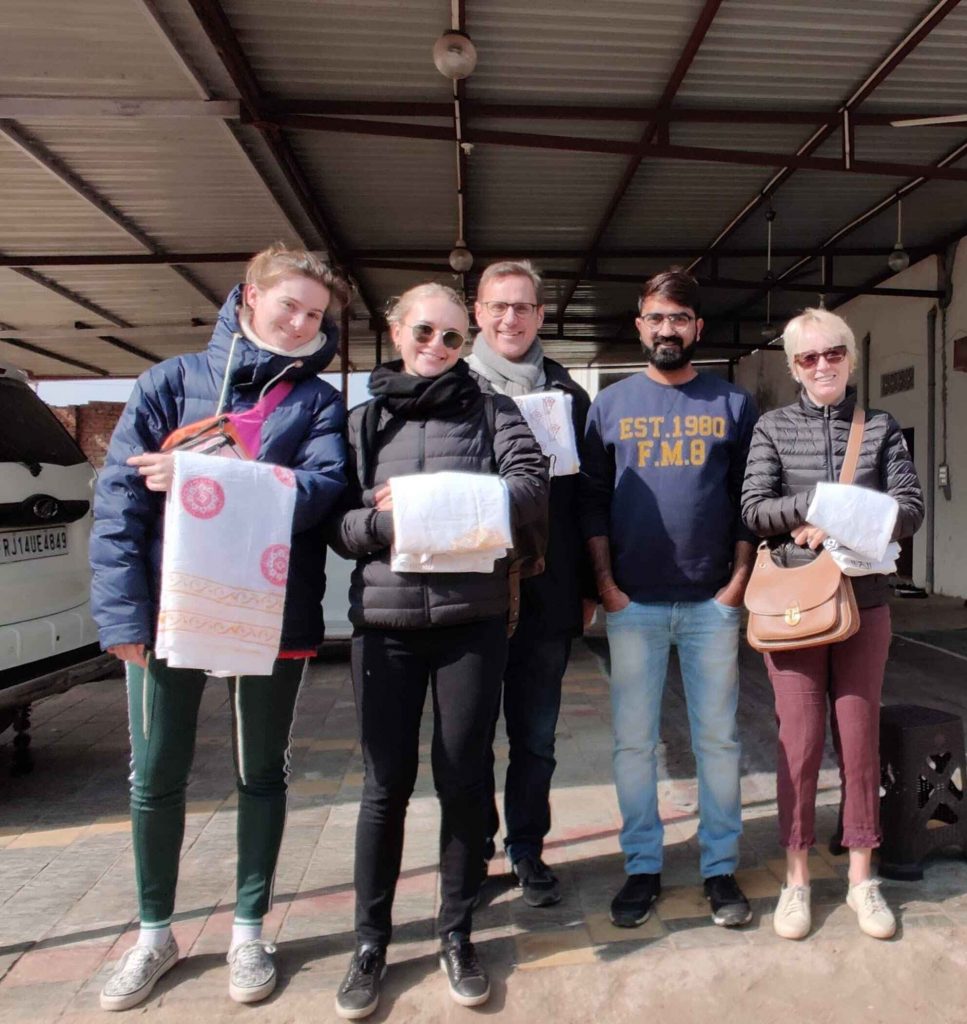